第1章 3つの挑戦
11年ぶりに新型ロータリーエンジンの生産を立ち上げる
マツダは、2012年6月に「MAZDA RX-8」の生産を終了してもなお、既存の設備を使い、メンテナンスを繰り返しながら、補修部品として13B型ロータリーエンジンの生産・供給を続けてきました。しかし、構造や性能要件が異なる新しいロータリーエンジンの生産を立ち上げるのは実に11年ぶりのことです。そこには、大きく3つの挑戦がありました。
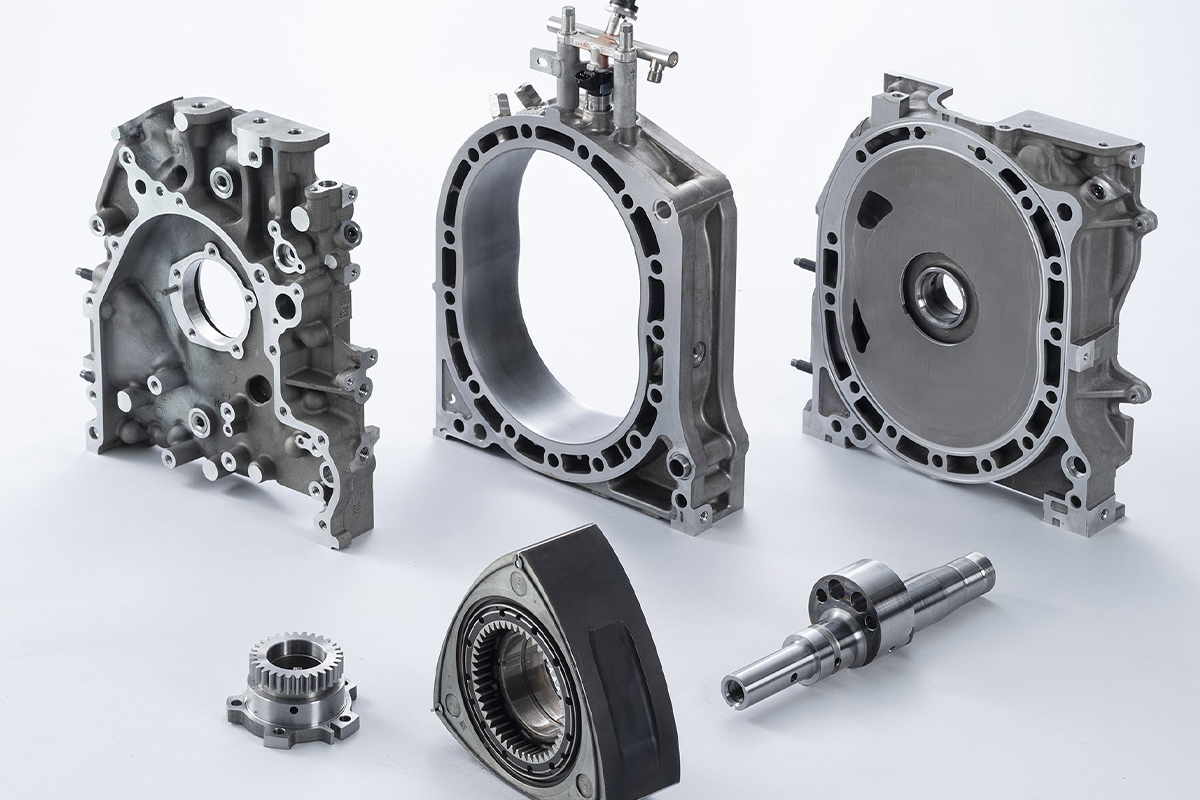
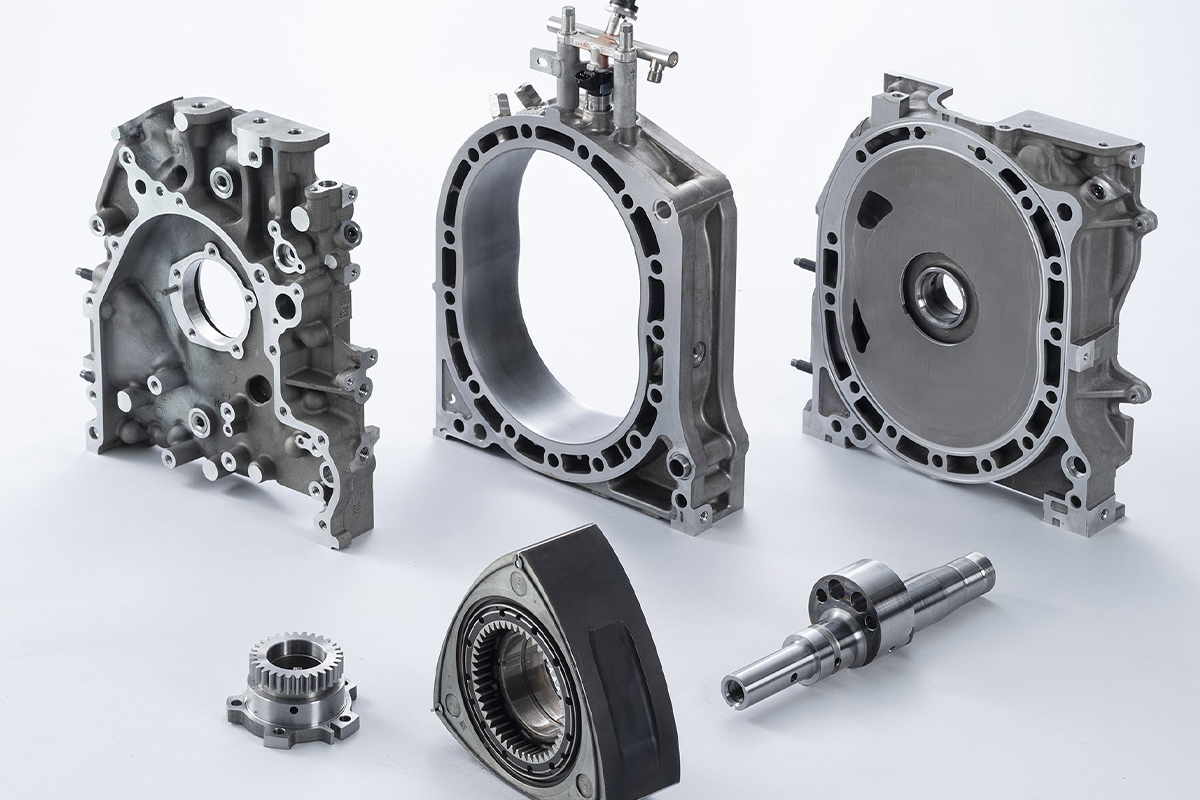
ロータリーエンジンを構成する部品
ロータリーエンジンを構成する部品
1つ目の挑戦は、「バランス精度の追求」です。8C型ロータリーエンジンは排気量830cc×1ローターの構成。排気量654cc×2ローターの13B型ロータリーエンジンに対して、創成半径は105mmから120mmに拡大し、且つシングルローター化しています。これは発電機として求められる出力を1ローターで発生させるために必要となるサイズである一方で、回転運動の半径は大きくなり、振動を互いに打ち消し合うローターがないため、振動面では決して有利な構造とは言えません。そこで求められるのが、ローターのバランスの精度です。8C型ロータリーエンジンの生産工程では、鋳造、機械加工、組立の各工程で一貫してこのバランスの精度を追求し、スムーズな回転の実現に取り組んでいます。
2つ目の挑戦は、「強くつくる」です。日常の幅広いシーンにおいてバッテリーEVとして使えるEV走行距離を確保するために重要なのが、軽量化です。軽量化への貢献のために8C型ロータリーエンジンで挑戦したのが、サイドハウジングのアルミ化です。今回サイドハウジングをアルミ化することで、エンジンの重量自体は約15kgの軽量化を見込んでいましたが、素材の強度が落ちる中で高速回転するローターと接する摺動面の強度をどのように確保するかが課題となります。そこで、エンジニアたちは、同じくアルミでできたSKYACTIVエンジンのシリンダーヘッドの鋳造技術をシミュレーション技術を活用してサイドハウジングの鋳造に最適化し、新たな溶射技術と組み合わせることで必要な強度を確保。こうして、約60年ぶりにアルミサイドハウジングが復活しました。
3つ目は、「フレキシビリティ」です。8C型ロータリーエンジンの機械加工工程を設計する際に生産技術エンジニアたちがこだわったのは、今までよりも精度良く機械加工が行えるようにするのはもちろんのこと、電動化の需要変動に対応できるポテンシャルを持ったフレキシブルなラインにすることでした。すなわち、8C型ロータリーエンジンの部品だけではなく、異なる車種や異なる部品の機械加工ができる生産ラインを目指しました。
11年越しの新型ロータリーエンジンの生産立ち上げのために、生産技術エンジニアと生産現場の工場が挑んだ挑戦。それは、受け継がれてきた技術をベースに、SKYACTIV技術で培ってきた最新のモノづくりの考え方や工法を取り入れながら、変わることなく匠の指先に伝わる感覚で品質を支えることでした。その挑戦のストーリーを新たに導入した生産技術と合わせてご紹介いたします。