第2章 素材工程
ローター --砂粒1つの精度で鉄を鋳込む--
ロータリーエンジンの象徴とも言える三角形のおむすび型のローターは、溶けた鉄を鋳型に流し込んで固める鋳造によって生産されています。ローターの重量バランス精度の追求はこの鋳型を成型するところから始まります。複数の砂型を組み合わせて作られる鋳型の中でも重要なのが、「中子」と呼ばれるローターの中空部を作るための砂型です。8C型ロータリーエンジンでは、この「中子」を生成する金型の構造を見直し、機械的なリンク機構からアクチュエータースライド式に変更することで、砂型と金型の間のクリアランスを従来の0.4mmから0mmに向上しています。
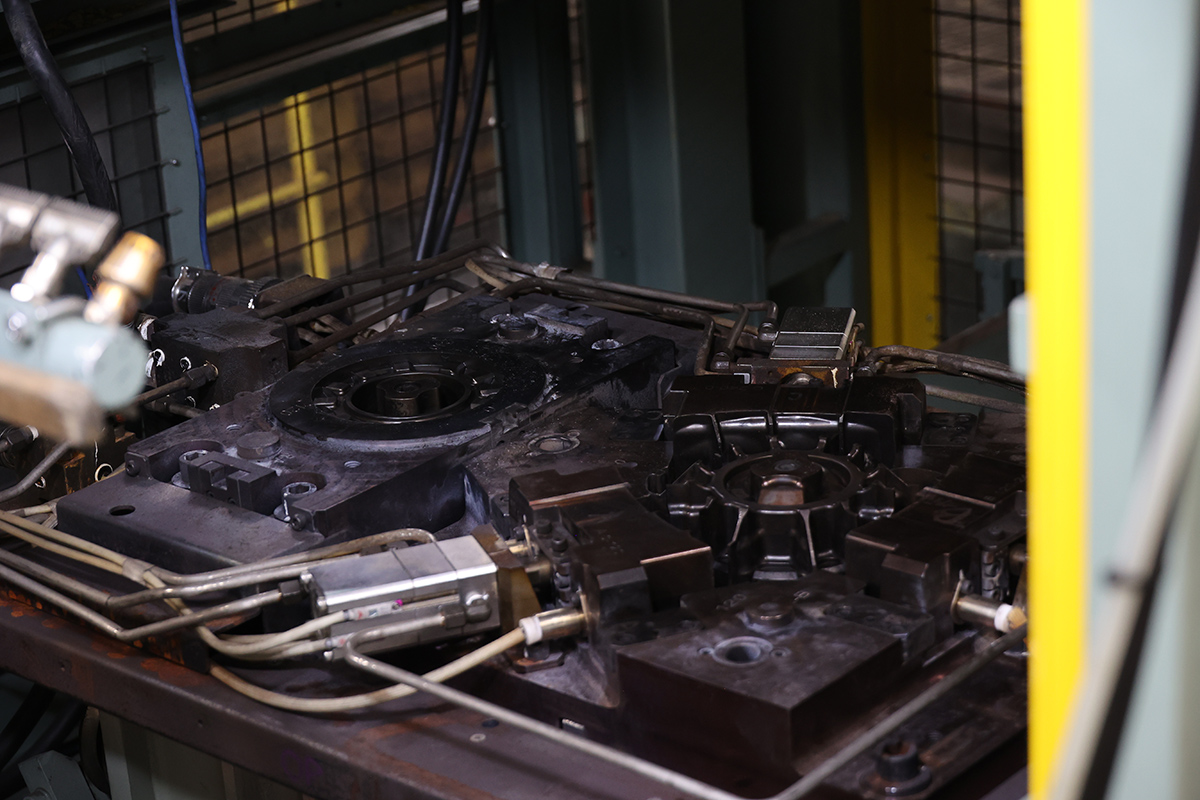
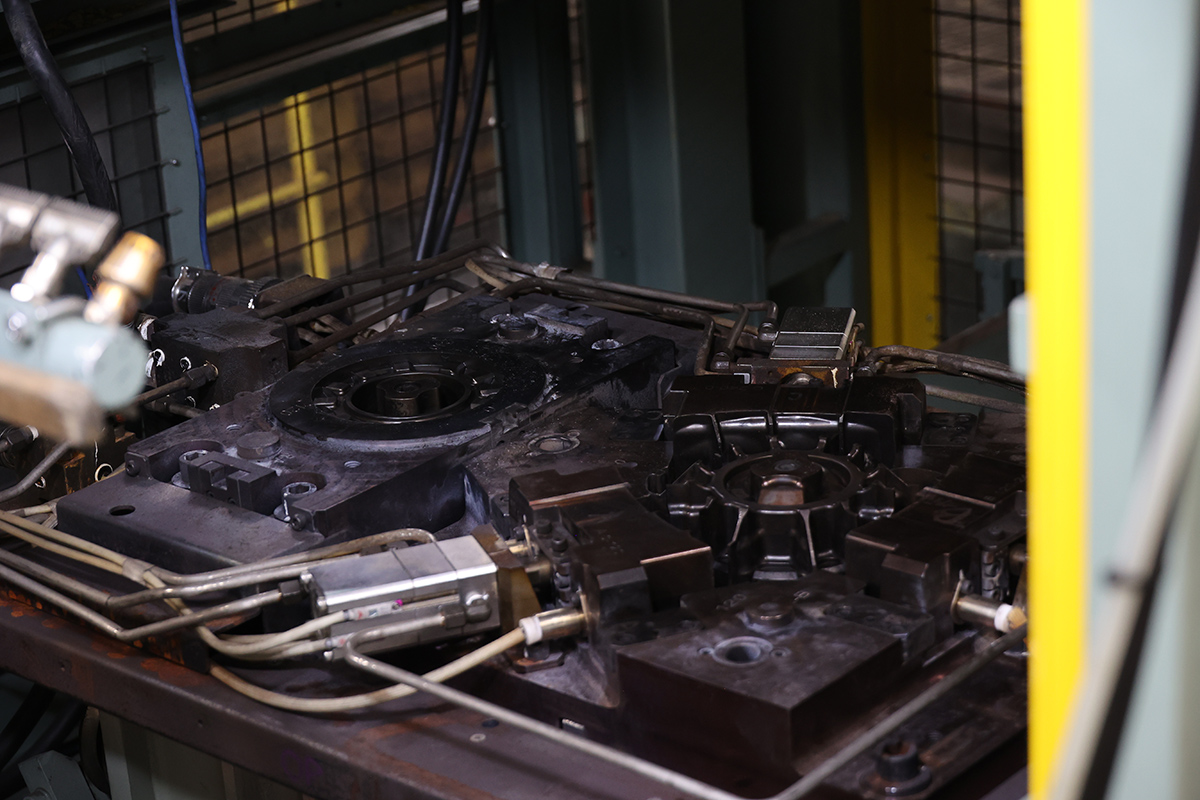
ローターの中子を生成する金型
ローターの中子を生成する金型
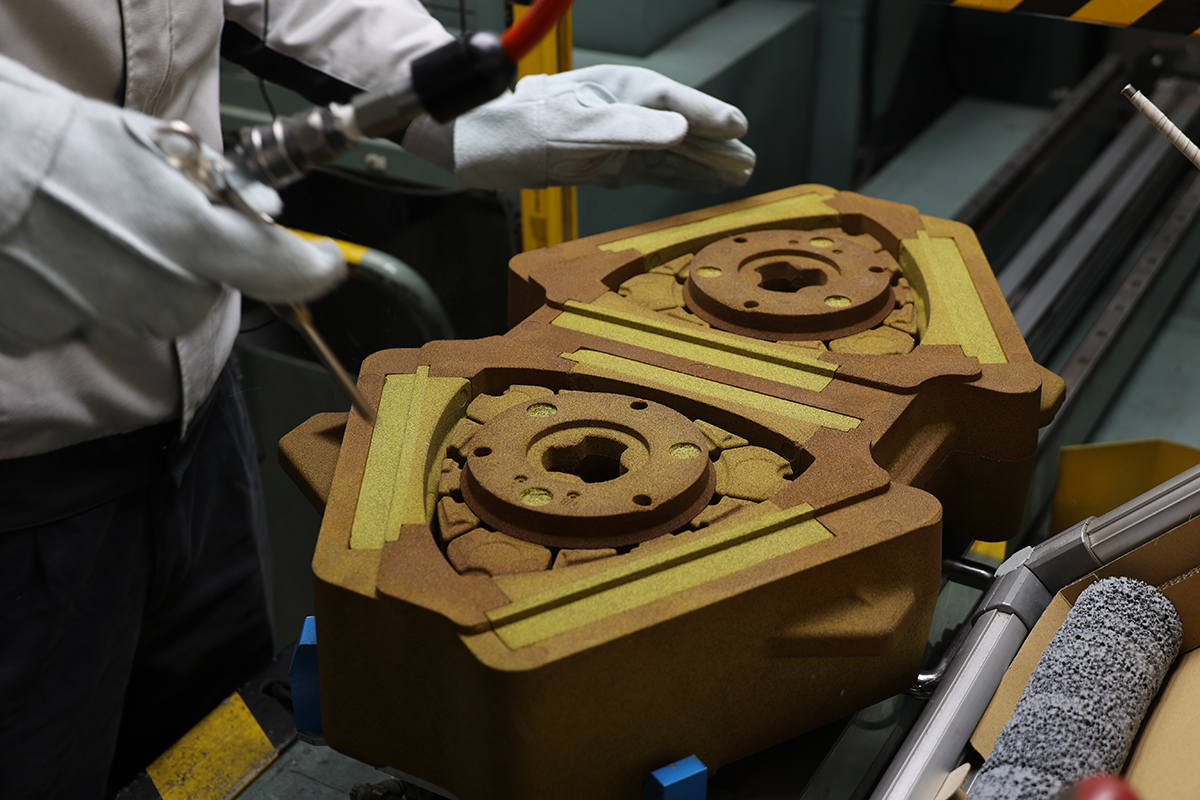
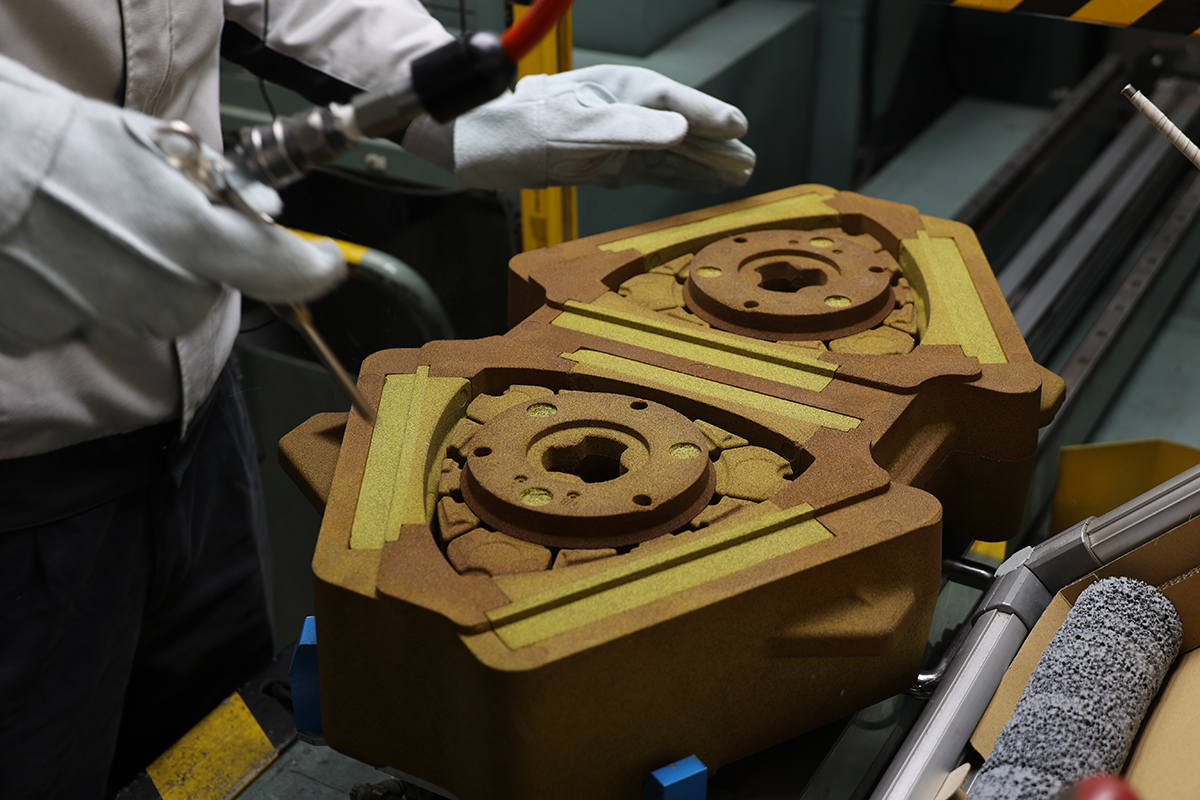
複数の砂型を手で組み合わせて鋳型が完成する
複数の砂型を手で組み合わせて鋳型が完成する
さらに、8C型では鋳型に溶けた鉄を流し込む作業を自動化しています。これまで、真っ赤に溶けた約1400℃の鉄を砂型に流し込む作業は、熟達した作業者による手作業でしたが、高熱に溶けた鉄の間近での作業は体力的に厳しく、そのため安定した品質を確保しにくい工程でした。そのため、今回は機械でその作業を行う技術を開発。これにより、鉄を流し込んだ後に生じる部位ごとの温度差を±10℃以内とする高精度な鋳込みが可能となり、熱収縮変形量のバラツキを抑えることにも貢献しています。
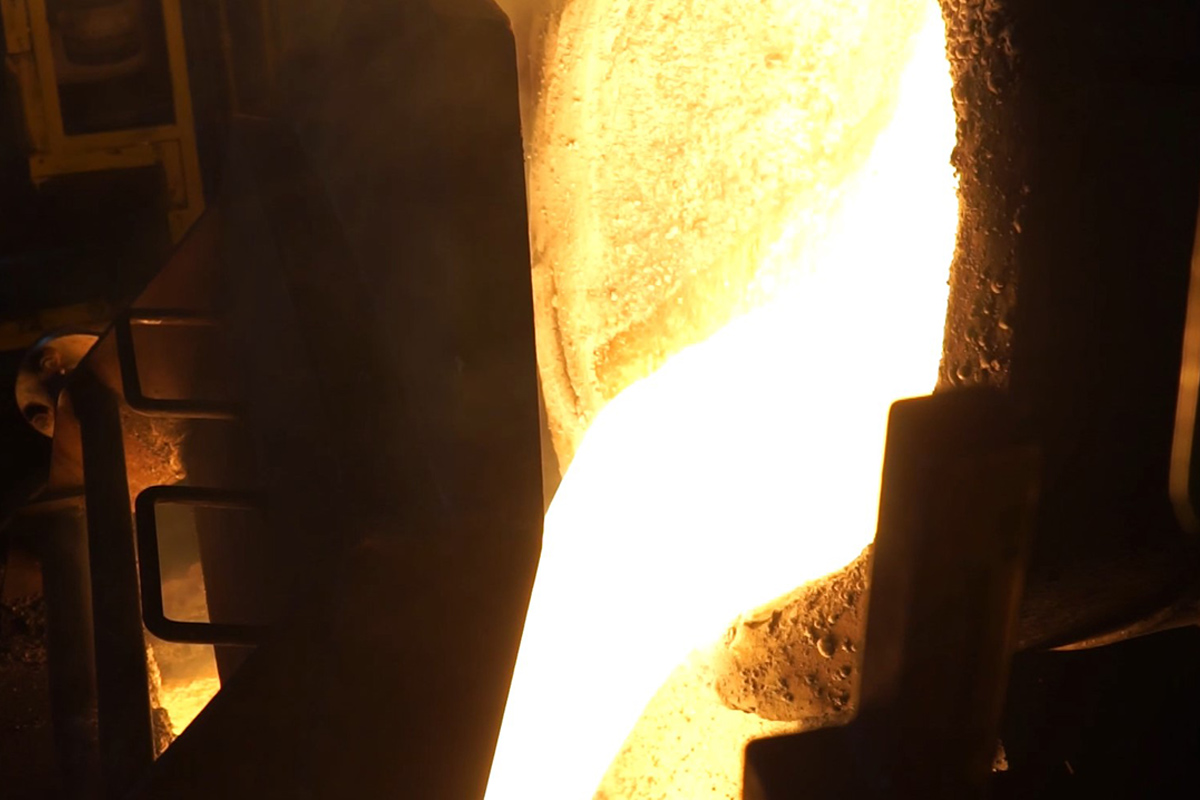
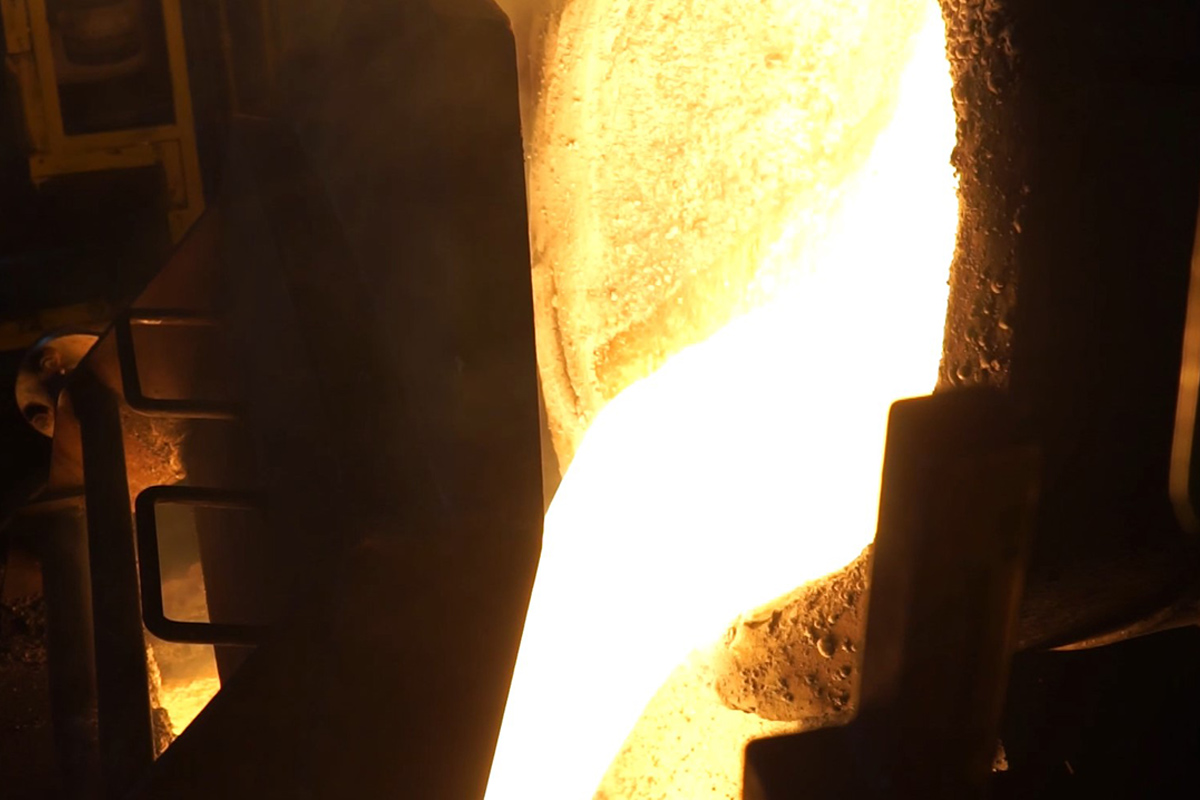
溶けた鉄を鋳型に流し込む様子
溶けた鉄を鋳型に流し込む様子
ローターハウジング –-最新のダイキャストマシンによる高精度な鋳造--
レシプロエンジンのシリンダーブロックにあたるローターハウジング。その生産は、内壁面を構成する鉄製シートメタルの成形から始まります。まゆ形に成形されたシートメタルを、ダイキャスト金型にはめ込んで、その外周に溶けたアルミを射出してローターハウジングを鋳造していきます。8C型では、緻密に制御しながら溶けたアルミを金型へ充填する最新のダイキャストマシンを新たに導入しました。金型内が高真空に対応したダイキャスト金型を使い、多関節ロボットを使用して溶けたアルミを充填しています。より緻密な制御を用いて、精度の高い鋳造が可能となりました。
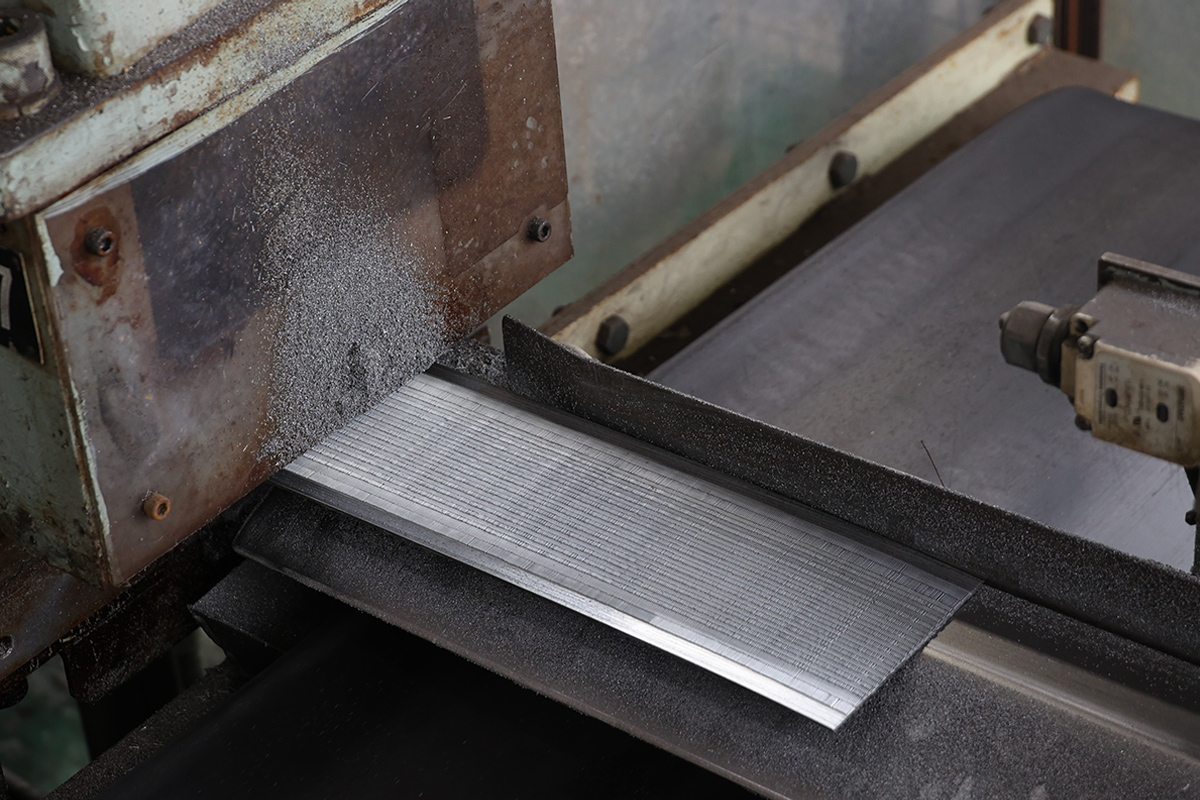
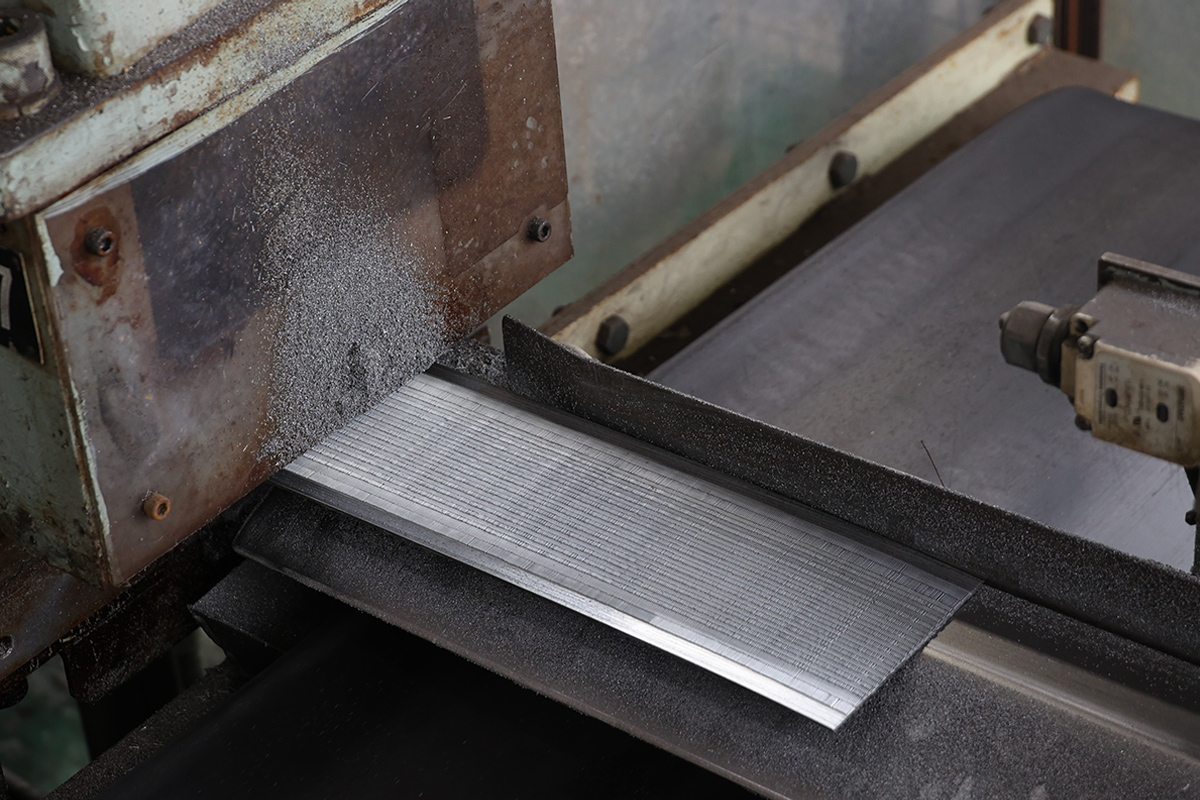
目立て後のシートメタル
目立て後のシートメタル
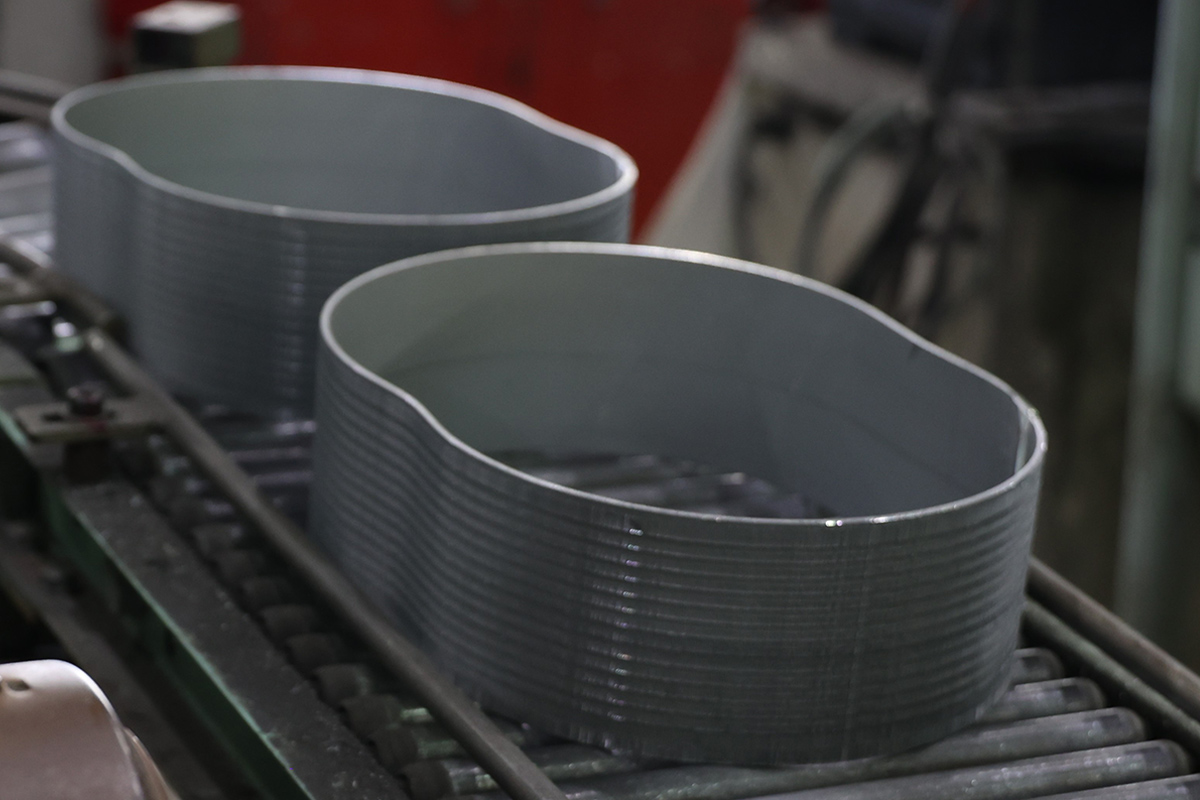
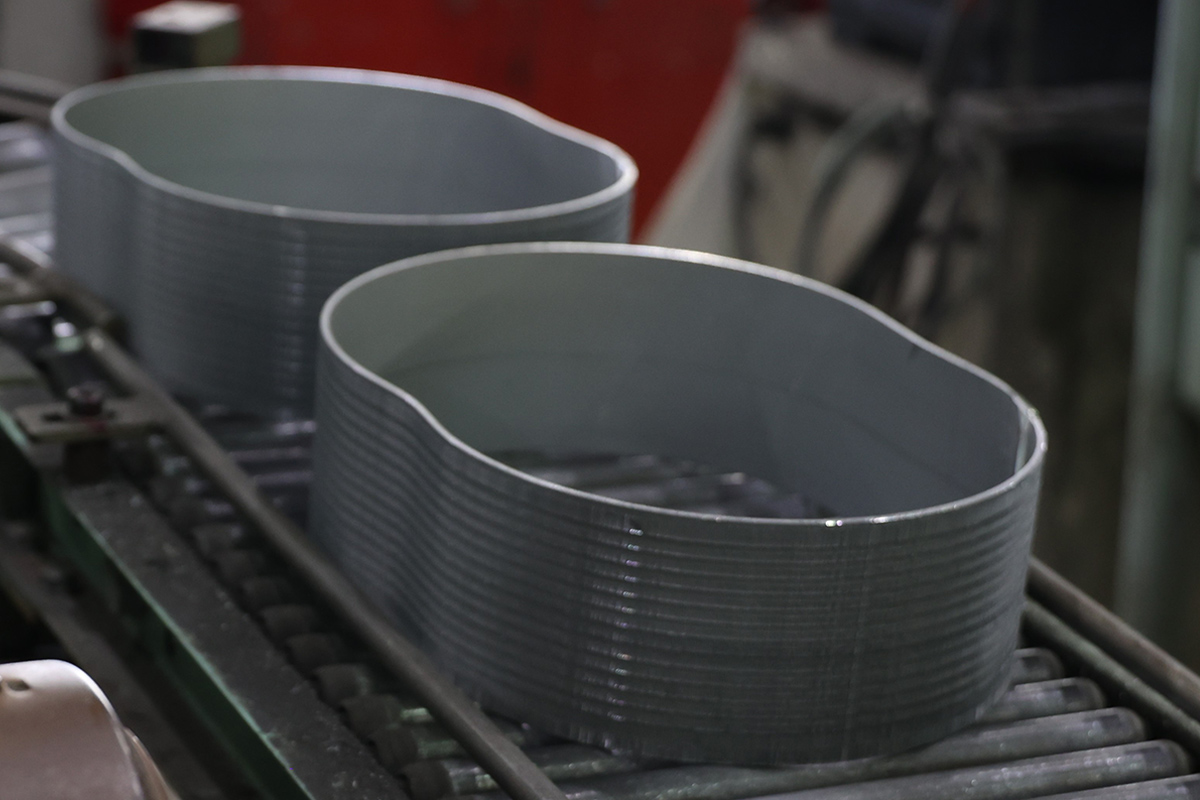
まゆ形に成形されたシートメタル
まゆ形に成形されたシートメタル
サイドハウジング --SKYACTIV エンジンの技術を応用してアルミ化と高強度化を両立--
ローターを挟み込む形で、高速で回転するローターの側面と接するサイドハウジングは、初期型のコスモスポーツに搭載した10A型を除いて鋳鉄で製造されてきました。今回の8C型では、エンジンの軽量化を図るために、サイドハウジングの素材を従来の鉄製からアルミ製へと変更し、エンジン単体で15kg以上(約20%)の軽量化を実現しています。一方で、従来の鋳鉄と比較するとアルミは強度が劣ります。そこで、採用したのがマツダ独自のAPMC(Advanced Precision Mazda Casting)法と呼ばれる鋳造方法で、SKYACTIVエンジンのシリンダーヘッドの生産で実用化した技術です。今回、C型ロータリーエンジンのサイドハウジングの薄肉で軽量な形状を実現できるアルミの充填方法を開発しました。そして、複雑かつ薄肉形状の部分は砂型でアルミを隅々まで行きわたらせ、強度が必要な摺動面には熱伝導率が高い冷却プレート(金型)をあてて急速に冷やして緻密な金属組織を形成することで、軽量化と高強度化の両立が可能となりました。
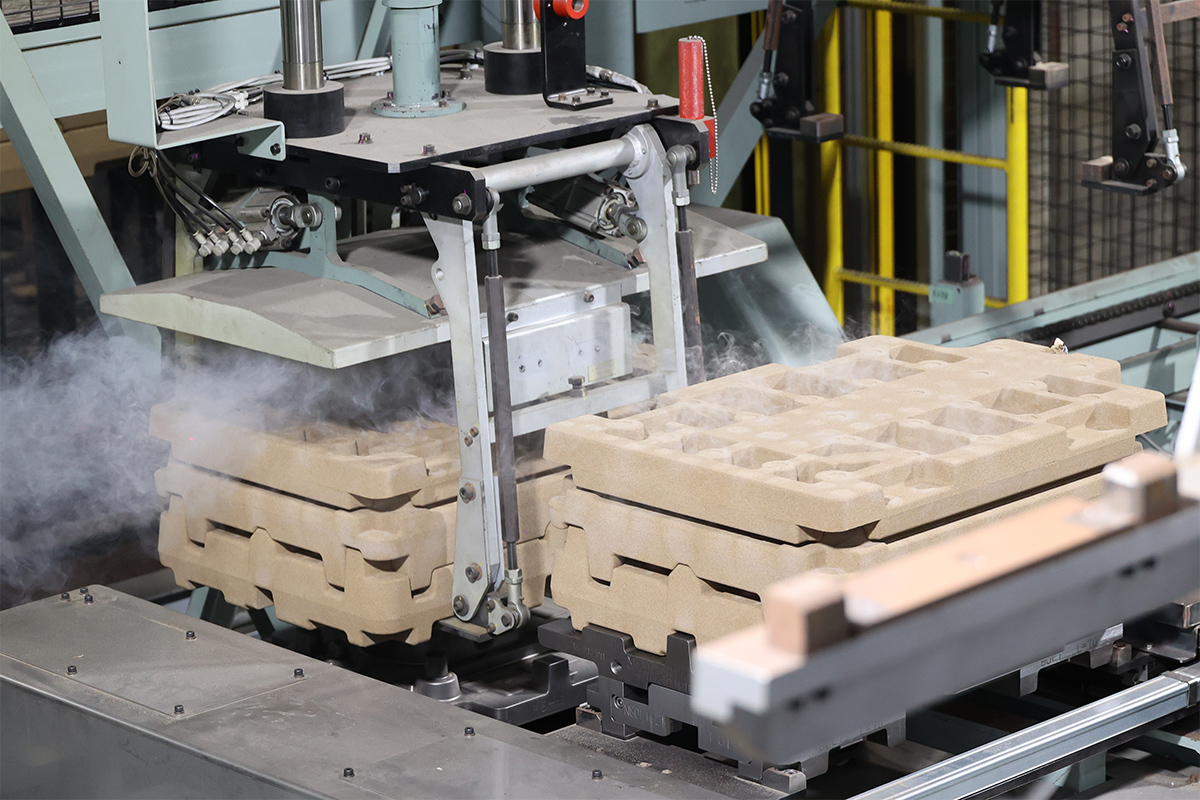
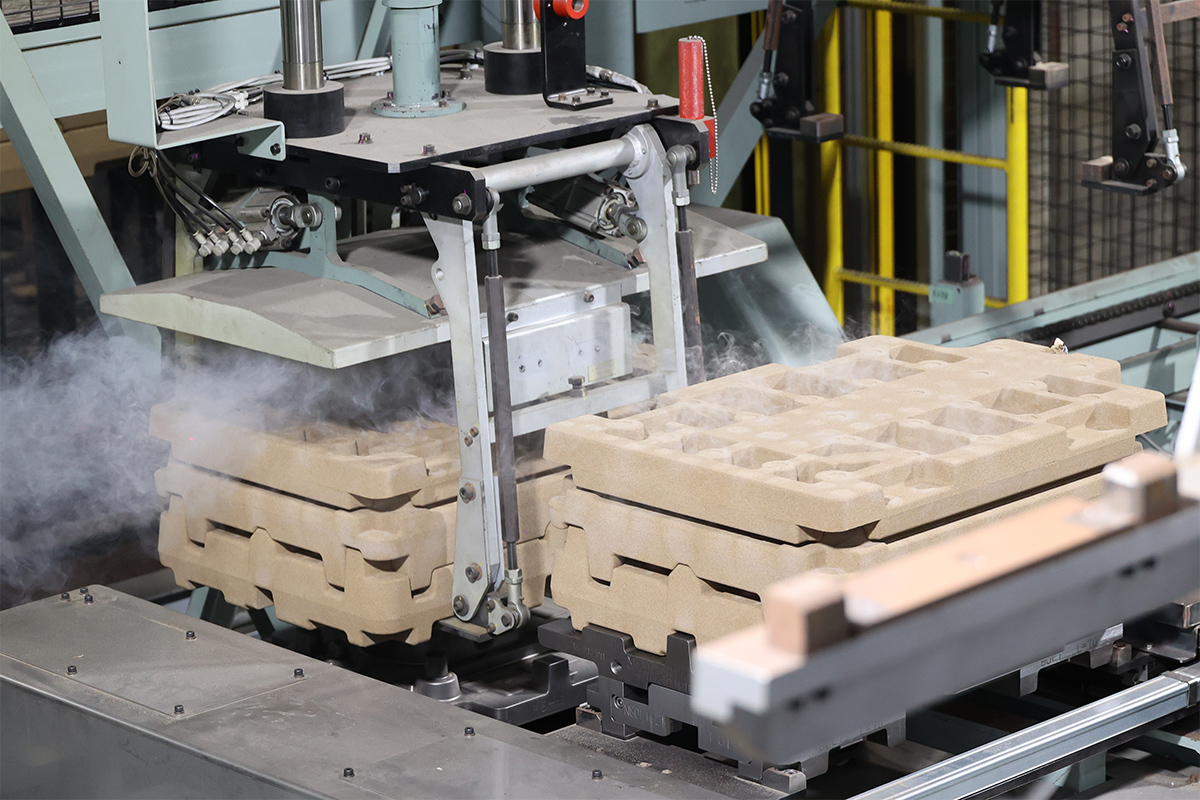
電磁ポンプでアルミの溶湯を充填する
電磁ポンプでアルミの溶湯を充填する