第3章 機械加工工程
ローター --工程集約による加工精度の向上--
素材工程で作られた各部品は、次に機械加工工程へと送られ、素材を切削して機能的に必要な溝や穴などを加工したり、加工面を研磨して表面を整えたりします。ローターの機械加工においても重要となってくるのは、重量バランス精度の追求です。工程ごとに切削・研磨を行っていく過程において、加工機の治具による掴み替えの度に小さなズレが生じます。そこで、8C型ロータリーエンジンでは、ローターの切削工程を従来の50工程から9工程に大幅に減らした工程を設計。掴み替え頻度が少なくなり、加工精度が向上しました。また、切削・研磨後に行うバランス調整の作業は、SKYACTIVエンジンの燃焼室を加工する計測補正加工技術を応用して自動化することでさらなるバランス精度の向上を図っています。従来は人の手で行っていたこの作業について、8Cではバランス測定で修正量を算出し加工機に転送、タッチセンサーでバラツキに合わせた補正量を決定し、エンドミルで調整加工を行っています。
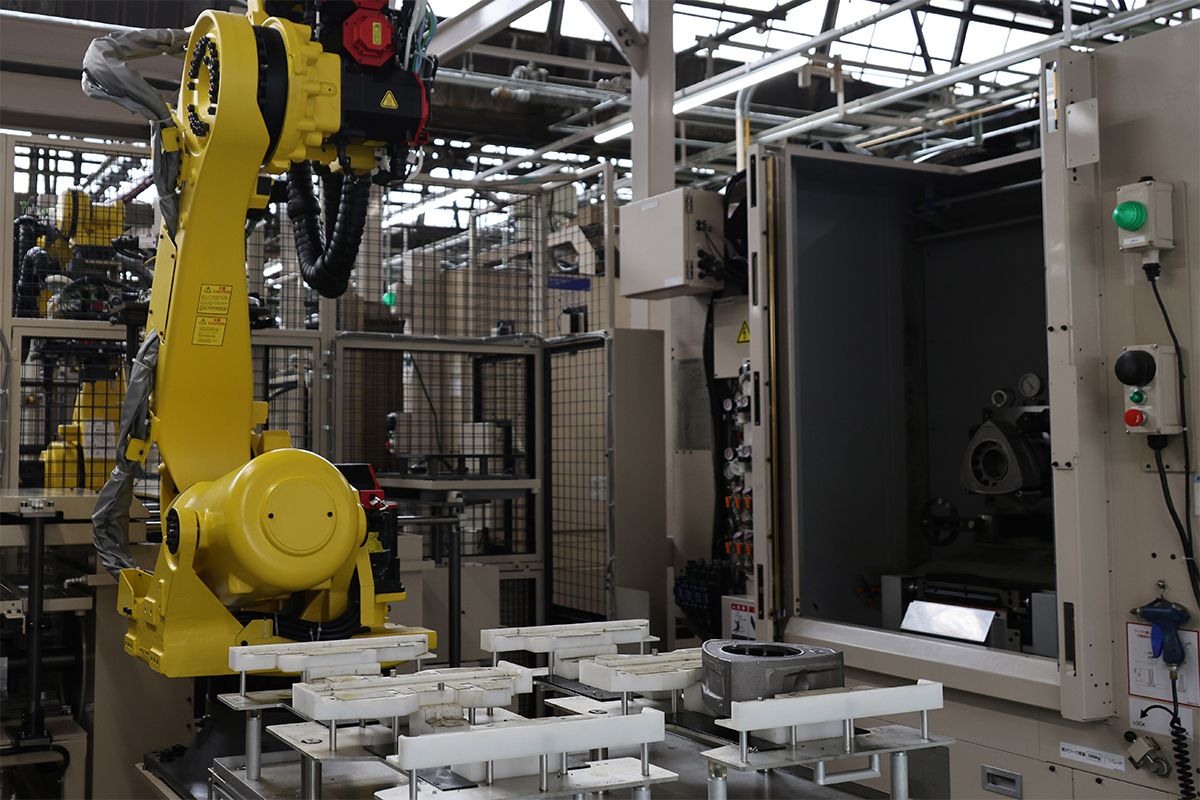
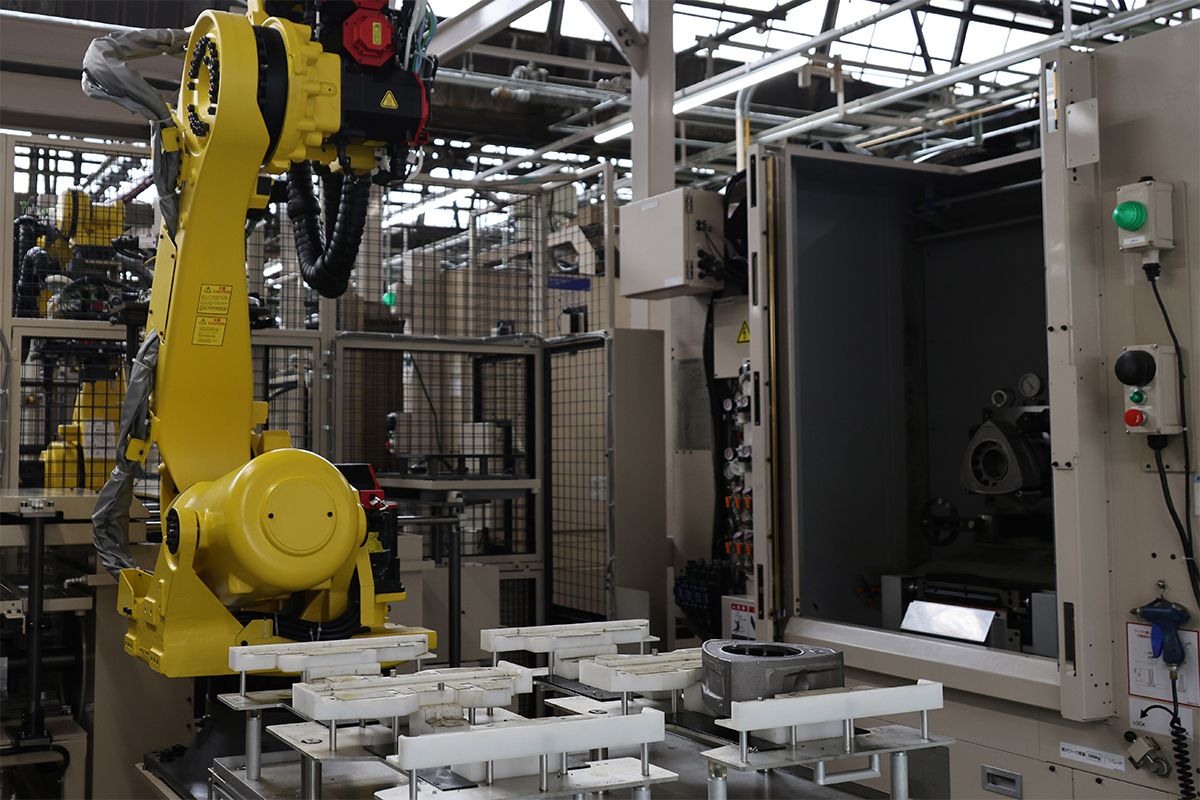
ローターの機械加工ライン
ローターの機械加工ライン
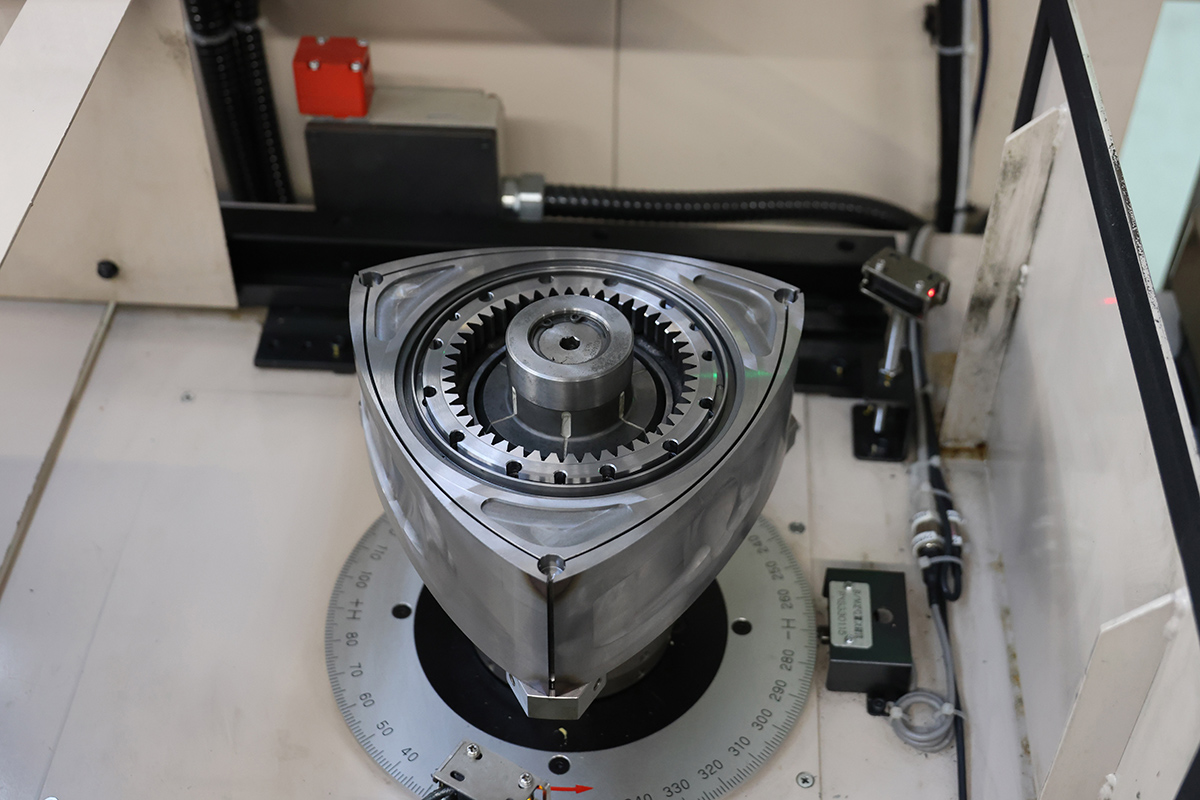
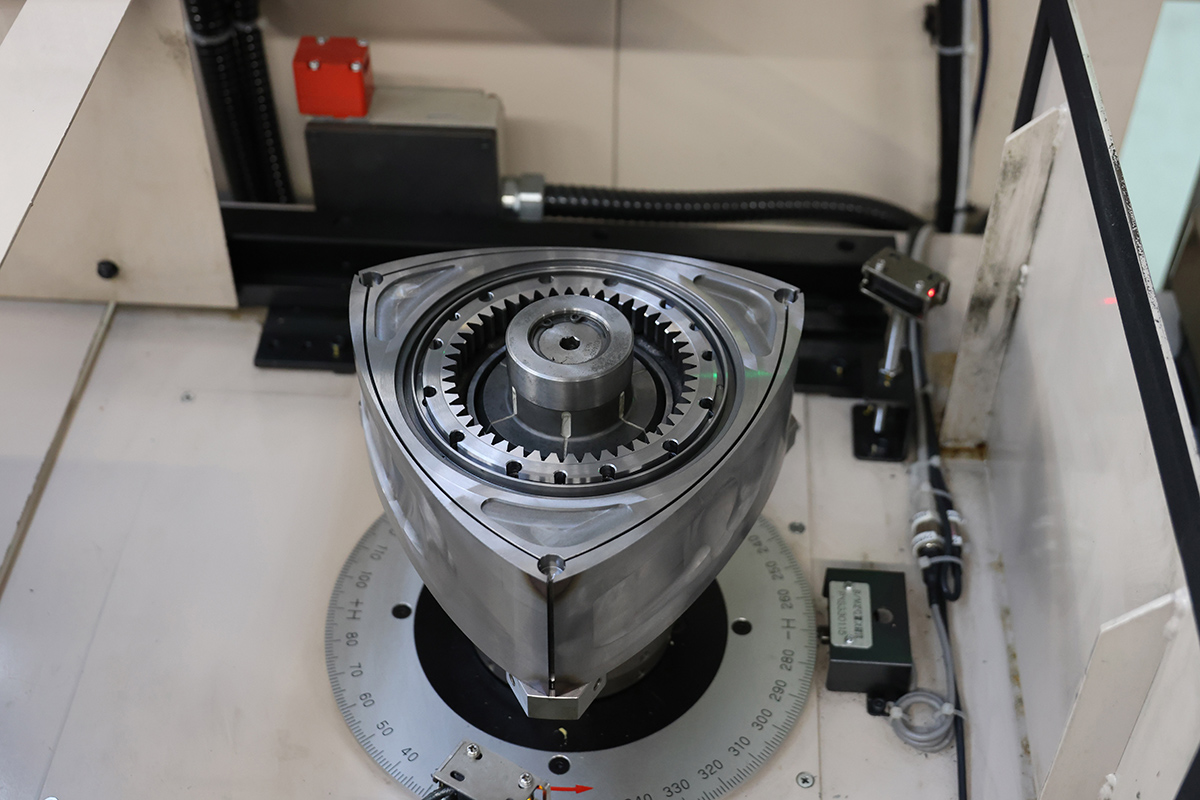
加工済みローターの重量バランス計測
加工済みローターの重量バランス計測
ローターハウジング --地元サプライヤーとの共創で先人のノウハウをデジタル化--
ローターハウジングは断面が特殊な形状をした部品です。そのため、その内壁面を研磨するホーニングマシンも、レシプロエンジンのシリンダーブロックを研磨する設備よりも複雑で専用のものが必要になります。8C型ロータリーエンジンのホーニングマシンの導入にあたっては、補修部品として出荷を続けている13B型と設備を共用化するために、フレキシビリティを向上させた新たなホーニングマシンを導入する必要がありました。その鍵となるのが、数値制御(NC)プログラムによるデジタル化されたホーニング加工です。それぞれのローターハウジングに応じて、砥石やローターハウジングを動かす複数の軸を同期させながら最適なホーニング加工が可能になります。しかし、ローターハウジングという特殊な形状の部品のホーニングマシンをデジタル制御するのは前例がない試みであり、長らく新たな設備の導入がなかったため、社内でもノウハウが乏しかったのです。この課題解決に協力いただいたのが地元広島の企業の方々です。かつてロータリーエンジンの加工機の設計などに携わった方々の経験やノウハウをヒアリングし、40年前に導入されて最近まで使用されていた13B型用の量産設備や古い試作用設備の実機調査を行いました。そして、そこから得られた知見や調査結果などを参考にしながら、NCプログラムのチューニングを繰り返したのです。地元企業との共創によって、8C型と13B型の共用化を実現した新たなホーニングマシンの導入に漕ぎ着けました。
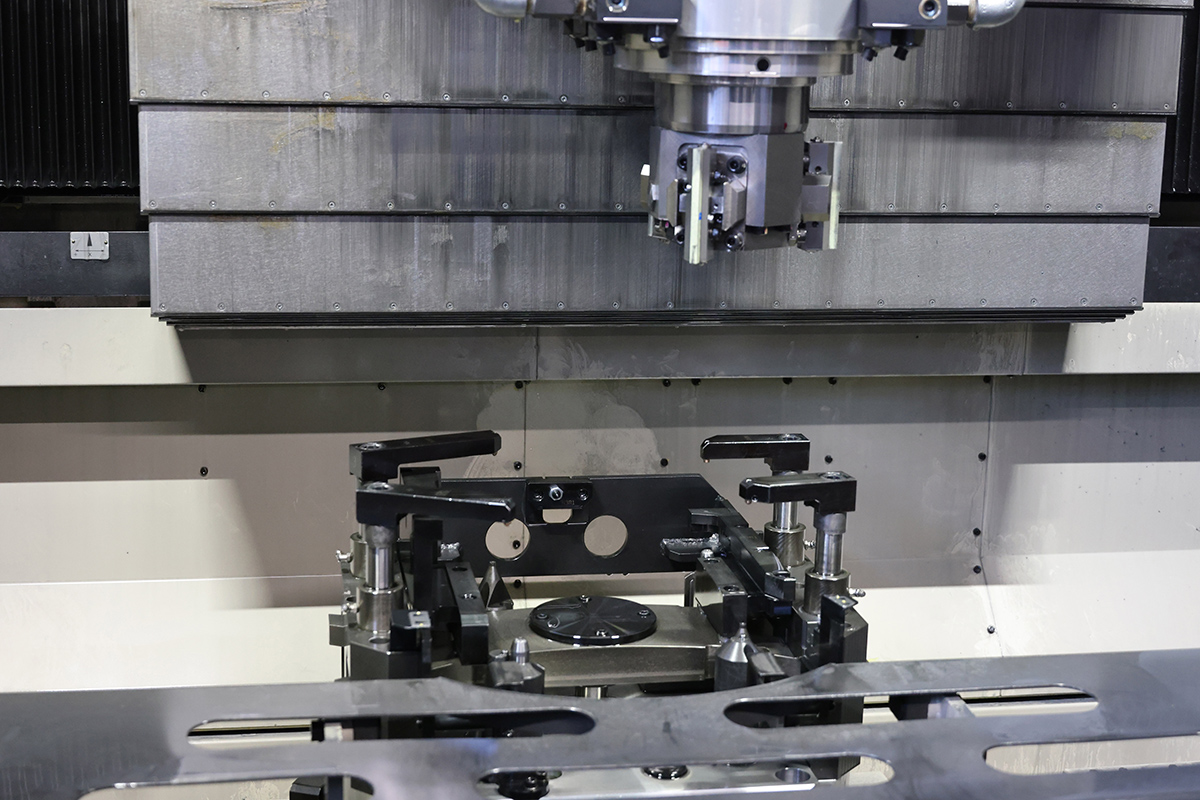
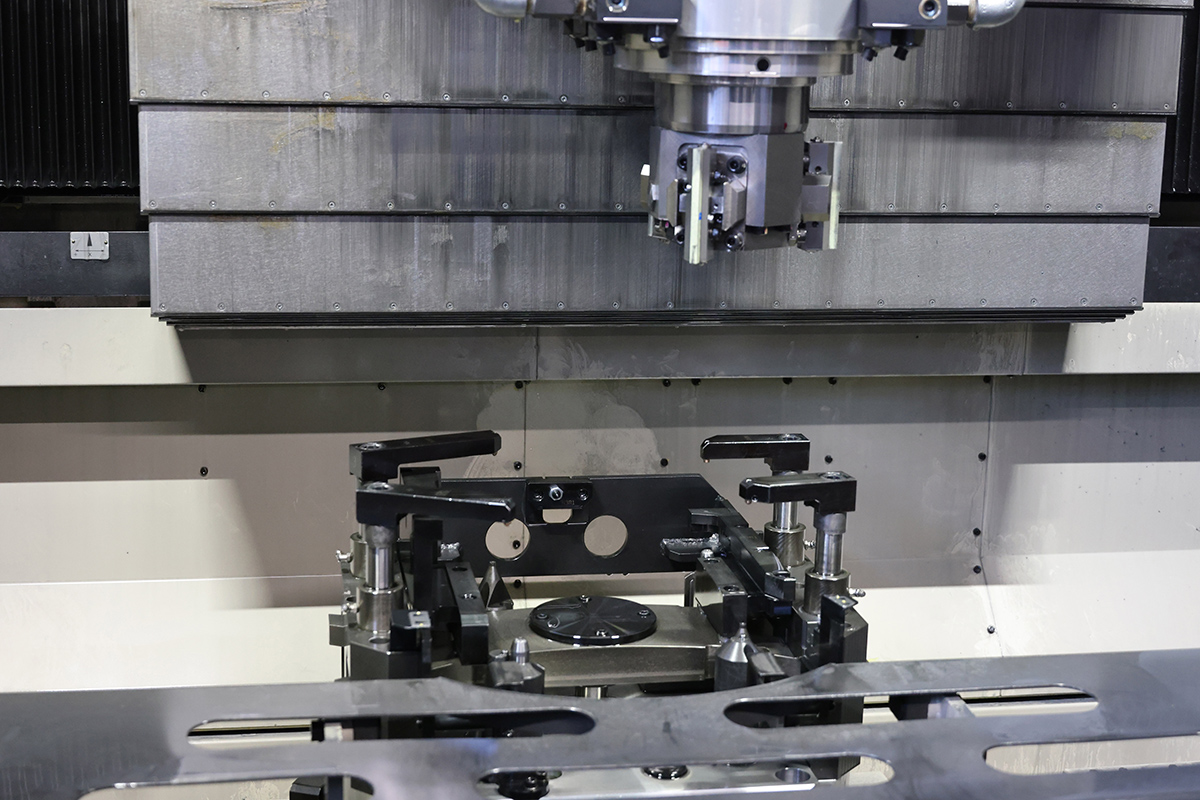
8C型と13B型のローターハウジングの研磨ができるホーニングマシン
8C型と13B型のローターハウジングの研磨ができるホーニングマシン
サイドハウジング --新たな溶射技術で摩耗を低減--
8C型ロータリーエンジンのサイドハウジングのアルミ化にあたっては、ローター側面にあるサイドシールやオイルシールと、サイドハウジング間の摺動時の摩耗や、オイルシールとの馴染み性低下によるオイル消費の悪化が課題となります。そこで、耐摩耗性が高いことに加えてオイルシールとの馴染みも良い、高速フレーム法によるセラミック溶射をサイドハウジングに施すことで、摩耗と摩擦抵抗の低減を図り、オイルシールの機能を確保しました。高速フレーム溶射は、コーティング材料を高速火炎で加熱して溶融させ、超音速にまで加速し、素材の表面に衝突させて、偏平に潰れた粒子を凝固・堆積させることにより緻密な皮膜を形成するコーティング技術です。アルミサイドハウジングの溶射では、試行錯誤を重ね、裏側からエアーで冷却したり、あえて広い範囲にスプレーするなどの工夫を行い、柔らかいアルミ素材を変形させることなく、均一に膜を形成できる工法を実用化しました。この技術により、素材を鋳鉄からアルミに変更したにもかかわらず、サイドハウジングの摺動面の表面硬度を、従来よりも向上させることに成功しています。
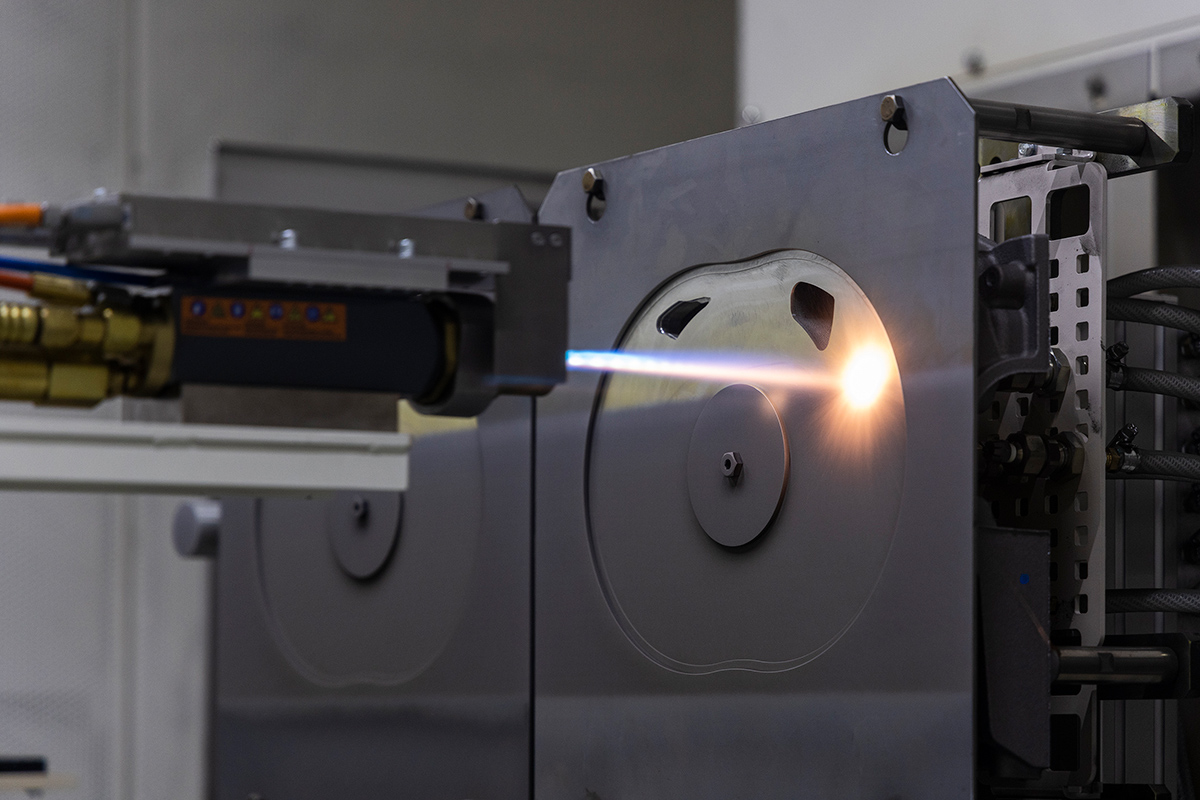
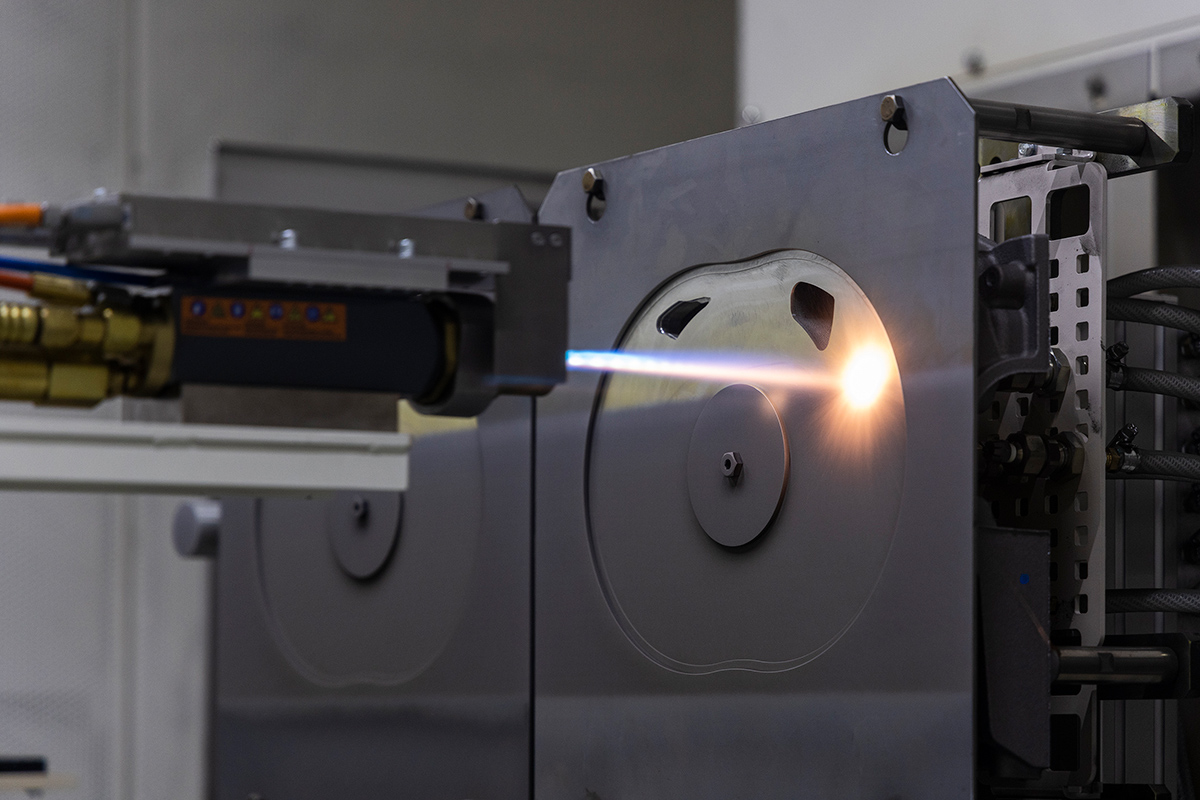
高速フレーム法によるセラミック溶射の様子
高速フレーム法によるセラミック溶射の様子